In the historic quest to bring samples from across the solar system back to Earth, the best mantra for success may be a simple, familiar phrase: “practice makes perfect.”
At least, that’s the feeling from recent dry runs of the grand finale of NASA’s OSIRIS-REx, an acronym for the megamouthful Origins, Spectral Interpretation, Resource Identification, Security-Regolith Explorer. Launched in September 2016, OSIRIS-REx is the first U.S. mission to snare a sample from an asteroid. In October 2020 the spacecraft dutifully gathered bits and pieces of the space rock Bennu, an ancient rubble pile of diverse leftovers from the early days of the solar system’s creation about 4.5 billion years ago. Now, it’s en route back to Earth, seeking to return that precious payload safely to terra firma in a thrilling act of interplanetary derring-do set to unfold in the early-morning hours of September 24.
At the heart of this effort is perhaps 250 grams (no one knows exactly how much yet) of extraterrestrial freight that was grabbed from Bennu using the novel Touch-and-Go Sample Acquisition Mechanism (TAGSAM), which also stores the sample. That hardware is cocooned within a sample-return capsule that OSIRIS-REx will cast off with split-second precision as it zooms by Earth. After enduring a fiery reentry targeted for the Department of Defense Dugway Proving Ground in the Utah Test and Training Range, roughly 70 miles west of Salt Lake City, the capsule should slow its descent via parachute and touch down somewhere within that remote swath of high desert—presuming, of course, that everything proceeds according to plan.
On supporting science journalism
If you're enjoying this article, consider supporting our award-winning journalism by subscribing. By purchasing a subscription you are helping to ensure the future of impactful stories about the discoveries and ideas shaping our world today.
To prepare for all plausible scenarios, nominal and otherwise, in late June and again early this month a cadre of scientists, engineers and other support personnel gathered for high-fidelity, step-by-step simulations of the OSIRIS-REx capsule retrieval and transport to a mock clean room.
June’s dry run was organized by Lockheed Martin—which built TAGSAM, the return capsule and OSIRIS-REx—and occurred at the company’s campus in Littleton, Colo., under the watchful eyes of planners scribbling notes for other missions. Foremost among these is the multiagency Mars Sample Return program—an even more ambitious and fraught multibillion-dollar effort that seeks to deliver Red Planet materials back to the Earth in the 2030s.
Edge of the Ellipse
There are good reasons for the OSIRIS-REx team to be on edge. The same stretch of Utah landscape that will shape its mission’s fate in a few months’ time has already been witness to both calamity and victory.
In September 2004 NASA’s Genesis spacecraft, toting samples of solar wind, failed to deploy its parachutes after atmospheric reentry. Because of improperly installed parachute-deployment switches, the high-speed impact led to a severely banged-up capsule and the contamination of its prized shipment. Fortunes turned less than two years later, in January 2006, when NASA’s Stardust mission successfully parachuted to Earth a capsule sprinkled with particles spewed by Comet P/Wild 2, providing a rich bonanza of material for subsequent laboratory scrutiny.
Significant work has gone into avoiding a “Genesis-level” event, says Richard Witherspoon, lead of Lockheed Martin’s OSIRIS-REx ground-recovery operations. “We’re confident that won’t happen again. We understand the technical issue that occurred on Genesis. We have done extensive testing on OSIRIS-REx to make sure that wouldn’t happen.” The design of the OSIRIS-REx capsule and recovery procedures are based on Stardust heritage, he adds.
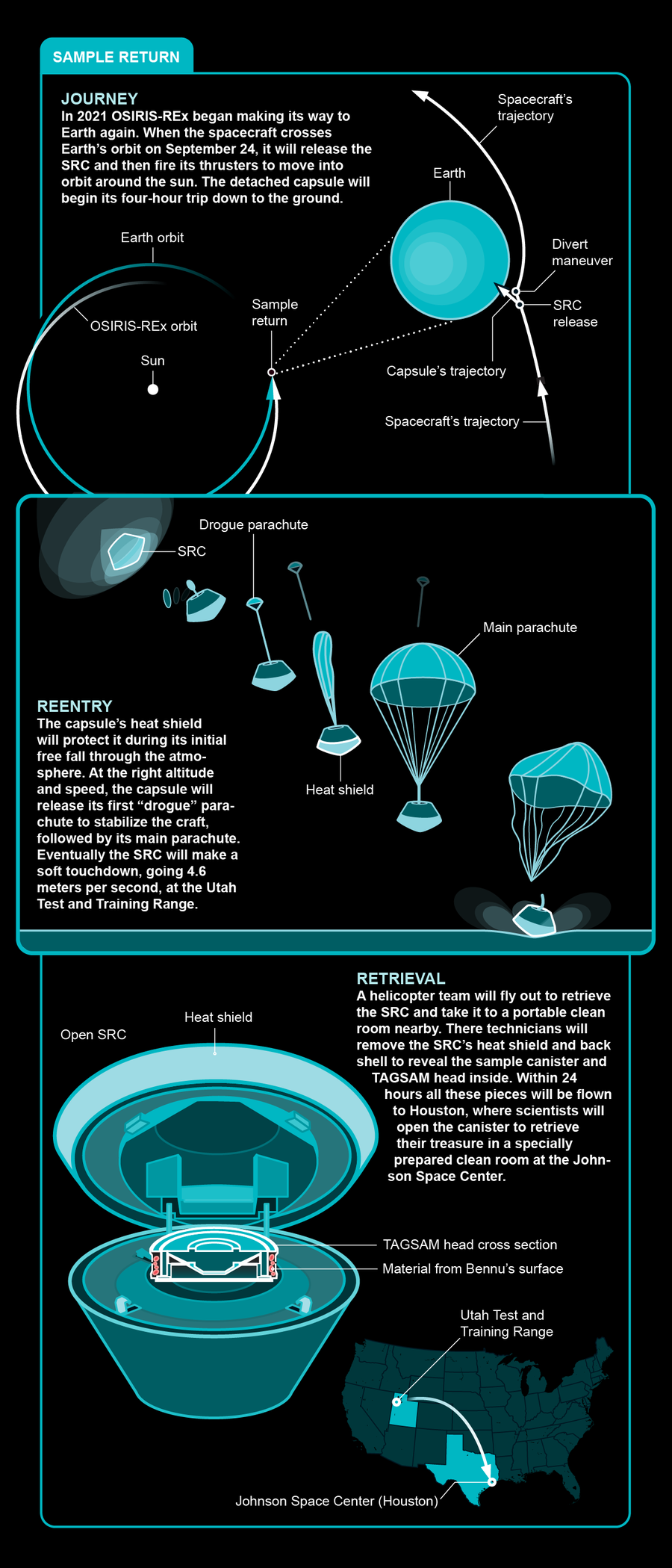
Credit: Jen Christiansen; Sources: “OSIRIS-REx, Returning the Asteroid Sample,” by Thomas M. Ajluni et al. IEEE Aerospace Conference Paper, March 2015; and “OSIRIS-REx: Sample Return from Asteroid (101955) Bennu,” by Dante S. Lauretta et al., in Space Science Reviews, Vol. 212; August 2017 (primary references)
Nevertheless, Witherspoon notes that the landing carries unavoidable risks—even at a slow 10 miles per hour under parachute. An unlucky landfall on a rock could breach the outer part of the capsule’s heat protective shield—although that situation is not expected to compromise the sample-carrying canister itself. Other less-than-ideal circumstances would involve finding the capsule upside down or retrieving it from a mushy mud puddle formed from rare desert rainfall.
The capsule’s drop area in Utah is an ellipse that measures 36 by 8.5 miles. On the nail-biting day, it will be ringed by four helicopters ready to transport a dozen or more recovery team members once the capsule’s touchdown site is pinpointed within. A systems safety officer will be among the first on the scene. They will check for any breaches or outgassing from the capsule to assure both the area and the payload are safe and sound for a soon-to-follow entourage of personnel.
“We have created conditions that were significantly worse just to make sure that we knew how to handle any scenario,” Witherspoon says. “We expect to have the capsule back to the clean-room processing area within two hours of it being on the ground and to have it on nitrogen purge within another two hours.”
That nitrogen flush will be done to assure outside air doesn’t pollute the samples prior to relocating the capsule and its high-value contents to NASA’s Johnson Space Center in Houston, Tex. Once there, the capsule will be fully disassembled, with removal of TAGSAM and the load of asteroid goodies occurring in freshly updated clean-room facilities.
While the June dry run had recovery team members practicing the handling of a mock return capsule and delivery to a simulated clean room, the second session (which took place from July 18 to 20) was on location in the area of the Utah desert where the asteroid samples will arrive. The latter session included helicopter training for recovery team members tasked with airlifting the sample capsule.
“The Moment of Enormous Emotional Relief”
Dante Lauretta, OSIRIS-REx’s principal investigator at the University of Arizona, reels off a long list of possible pain points while observing June’s recovery rehearsal. The most concerning ones are those that any dry run’s meticulous planning and improvisational actions can’t properly address. First and foremost, the capsule must be autonomously released above Earth—a complex procedure requiring the cutting of cables and detonation of explosive “hold down” bolts. Internal batteries need to wake up and supply power. Parachutes packed way back in 2016 need to unfurl. A problem anywhere in that lengthy chain will easily result in TAGSAM being crushed like a beer can after a free-falling, high-speed nose-dive into the desert floor.
Lauretta isn’t really worried, however. “Quite honestly, I put us at 99 percent chance of mission success,” he says, underscoring all the painstaking prelaunch testing of hardware and spacecraft performance to date. Even so, “it will be the moment of enormous emotional relief to see our parachute open and that sample drifting safely down to Earth. Then I know we did it. At that point it’s all gravy.”
Even if OSIRIS-REx’s capsule suffers a Genesis-like hard landing, Lauretta and others on his team are confident they could still pull off some great science. “What we’re worried about is protecting the asteroid sample from Earth contamination,” says Anjani Polit, OSIRIS-REx’s mission implementation systems engineer at the University of Arizona. “All the effort, the many rehearsals and operational readiness tests that are higher and higher fidelity, that’s worked extremely well.”
Prime the Pumps
All the tender loving care and lessons learned from OSIRIS-REx are feeding into NASA’s major planetary-science undertaking for the 2030s: the Mars Sample Return (MSR) enterprise.
Specimens of the Red Planet are also destined for delivery to the Utah Test and Training Range. But there are differences, mostly driven by the hot-button issue of whether life-forms might exist on Mars—and thus potentially in the retrieved samples. Anything other than a nonzero prospect of hauling viable extraterrestrial organisms to Earth and introducing them to our biosphere raises the specter of what “planetary protection” specialists call “backward contamination.”
As now planned, the cone-shaped MSR Earth entry vehicle will fall through Utah’s skies without a parachute, ruggedized to endure the wallop of impact with the high-desert hardpan, as well as any subsequent rolling and bouncing. From there, a recovery team will treat it as potentially hazardous material, enclosing it in a protective container and then transporting it to a yet-to-be-built isolation facility, likely positioned outside of Utah.
For MSR, “we are very much leveraging a lot of the work that’s being done on OSIRIS-REx,” says Nick Benardini, NASA’s planetary protection officer. “We’re building up the necessary skill sets for what’s needed,” with public safety and high sample integrity for scientific analysis as the driving goals.
The process is complicated by MSR’s inherently international nature—both NASA and the European Space Agency are fleshing out the endeavor. And even on the U.S. side, Benardini explains, the mission is so complex that NASA must rigorously engage with a slew of interagency partners, from the Centers for Disease Control and Prevention and the Federal Emergency Management Agency to the Department of Transportation and the Department of Homeland Security.
“OSIRIS-REx allows us to prime the pumps,” Benardini continues, to get procedures, training and sample integrity methods worked out as early as possible. “It’s allowing everybody to have a Mars Sample Return mindset.”